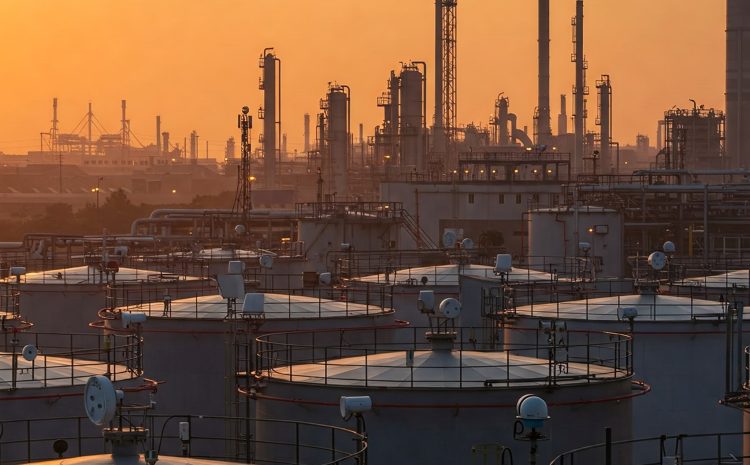
Optimizing Bulk Liquid Storage with Advanced Tank Farm Management Systems
Introduction
Efficient and safe management of bulk liquid storage is crucial in industries such as oil and gas, chemicals, and food processing. Traditional tank farm management systems often face challenges like manual monitoring, limited data accessibility, and inadequate safety measures. This case study explores the implementation of an advanced Tank Farm Management System (TFMS) that integrates wireless monitoring, real-time data access, and enhanced safety protocols to optimize tank farm operations.
Problem Statement: Challenges with Traditional Tank Farm Management
Many facilities rely on manual methods or outdated systems for tank level monitoring and inventory management, leading to several issues:
Manual Monitoring: Relying on manual dipstick measurements can be time-consuming and prone to human error.
Limited Data Accessibility: Without real-time data transmission, accessing current tank levels and inventory status is challenging, especially for remote monitoring.
Safety Concerns: Manual methods may not promptly detect high or low-level conditions, increasing the risk of spills, overflows, or shortages.
Addressing these challenges is essential to enhance operational efficiency, ensure safety, and reduce costs.
Solution Overview: Implementing an Advanced TFMS with Wireless Monitoring
To overcome the limitations of traditional systems, a comprehensive automation solution was implemented, incorporating the following key components:
Non-Contact Radar Level Transmitters:
Replacing manual dipstick methods, non-contact radar level transmitters provide accurate and reliable continuous level monitoring without physical contact with the liquid, reducing maintenance and potential errors.
Wireless Data Transmission:
Utilizing RF transmitters and receivers, the system wirelessly transmits real-time data from the tank farm to a central monitoring station, enabling remote access and reducing the need for on-site personnel.
Web-Based SCADA System:
A web-based SCADA system visualizes real-time data, allowing authorized users to monitor tank levels, receive alerts, and generate reports from any location with internet access.
Real-Time Reporting and Alarming:
The system enables immediate report generation and provides audiovisual alarms for high and low-level conditions, facilitating prompt corrective actions and enhancing safety.
Benefits of the Solution
The implementation of the advanced TFMS resulted in several significant improvements:
Enhanced Accuracy and Reliability: Non-contact radar level transmitters provide precise measurements, minimizing errors associated with manual methods.
Improved Operational Efficiency: Wireless data transmission and web-based monitoring eliminate the need for manual data collection and on-site inspections, saving time and resources.
Increased Safety: Real-time monitoring and immediate alarming for high and low-level conditions allow for timely interventions, reducing the risk of spills, overflows, or shortages.
Cost Savings: Reduced manual labor, minimized errors, and optimized inventory management contribute to overall cost reductions in tank farm operations.
Technical Architecture: How the System Works
The technical components of the solution work together to ensure effective tank farm management:
Data Acquisition via Non-Contact Radar Level Transmitters:
Radar sensors continuously measure liquid levels in tanks, providing accurate data without physical contact, suitable for various liquid types.
Wireless Data Transmission:
RF transmitters send data from the radar sensors to receivers connected to the central monitoring system, eliminating the need for extensive wiring and facilitating flexible system design.
Web-Based SCADA System:
The SCADA system aggregates data from all tanks, offering real-time visualization, historical data analysis, alarm management, and reporting features accessible via secure web interfaces.
Real-Time Reporting and Alarming:
The system generates real-time reports on tank levels and inventory status, and provides audiovisual alarms for predefined thresholds, ensuring prompt responses to critical conditions.
Results: Key Improvements After Implementation
Following the implementation of the advanced TFMS, the facility experienced several notable improvements:
Enhanced Data Accuracy: Automated radar measurements reduced human errors, leading to more reliable data for decision-making.
Operational Efficiency: Wireless data transmission and web-based monitoring reduced the need for manual checks and on-site presence, streamlining operations.
Improved Safety: Immediate detection and alarming of high and low-level conditions allowed for quick corrective actions, minimizing the risk of hazardous situations.
Cost Reduction: Optimized processes and reduced manual interventions led to significant cost savings in both labor and operational expenses.
Conclusion: The Future of Tank Farm Management
The implementation of an advanced Tank Farm Management System with wireless monitoring has transformed traditional tank farm operations by enhancing accuracy, efficiency, safety, and cost-effectiveness. By integrating non-contact radar level transmitters, wireless data transmission, and web-based SCADA systems, facilities can achieve real-time monitoring and proactive management of their tank farms. This case study demonstrates the substantial benefits of adopting modern automation solutions in industrial liquid storage management.
From Technology
How do you transform your business as technology advances? Stay ahead of the curve by embracing new innovations, from automation to AI.
From Consumers
As consumer habits evolve, businesses must adapt. Learn how market leaders are adjusting their strategies based on consumer insights to stay competitive in a changing landscape.